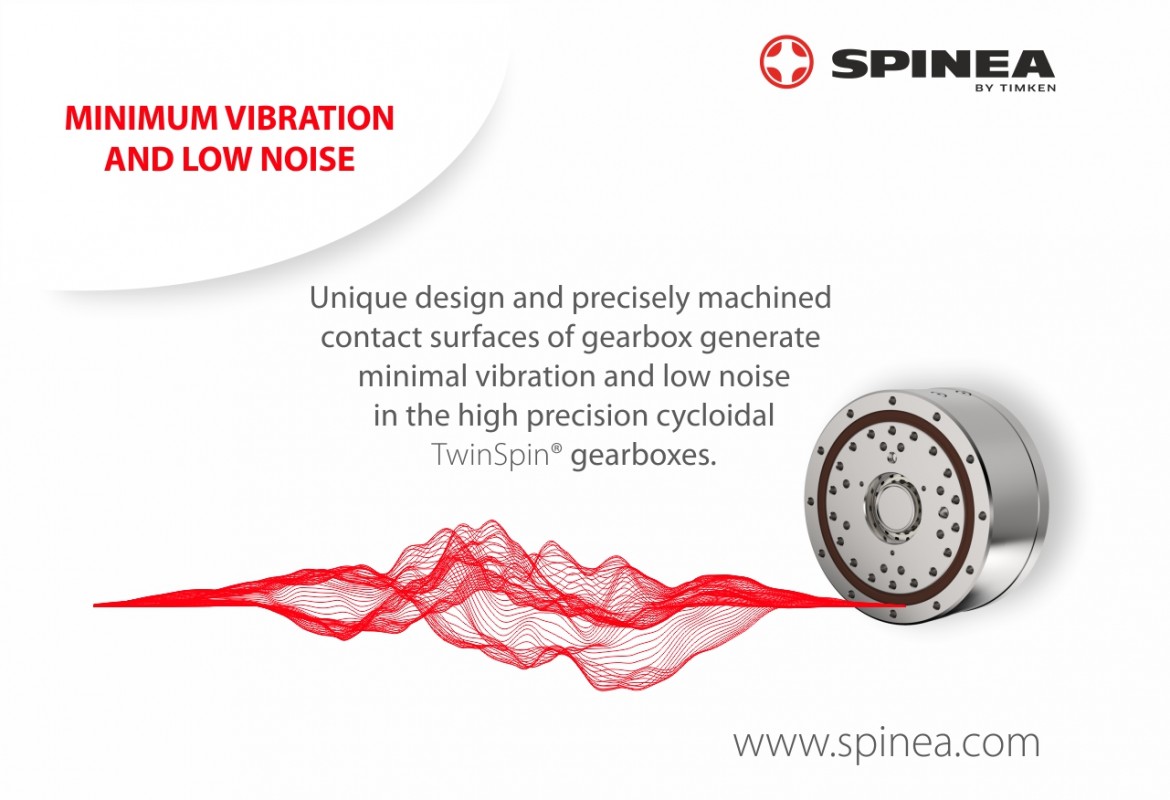
Cycles, vibrations, oscillations and frequencies are part of the existence of elementary particles, but also of cosmic objects and galaxies. They are integrated into inanimate matter, but also in biological creatures and groups.
In general, frequencies are energetic and informational in nature. They create, move, store, modify and transform energy along with the information that is integrated into their essence.
Scientists assume that just elementary particles at the level of quarks, electrons have an even deeper level, which is formed by "strings" having the same essence for all elementary particles, only they are created with different frequencies of oscillation of some universal matter. We know this theory as string theory.
Vibrations in the form of noise present the quality of the product. A low level of product noise is attributed to higher quality and more reliable product. Such a low noise level predisposes the product to be more balanced, with minimized sources of vibration, more precise fits, tolerances and roughness.
Higher vibration and noise levels also reflected in energy consumption, reducing product efficiency and consequently degrading product quality.
With these basic approaches, the TwinSpin® backlash-free cycloidal high-precision gearbox was also designed. It is characterized by a maximally balanced internal design that, while containing eccentrics as vibration generators, are positioned to eliminate their resulting effect during rotation. The gear mechanism itself is dominated by rolling friction, which inherently does not generate vibrations as is the case with shear friction. Balance and low vibration have also been achieved by single-stage gearing, which also achieves high gear ratios. Dimensional tolerances, geometric accuracy and roughness are extremely low, below 1 µm. The design and precision surfaces have created this significantly low noise SPINEA® cycloidal gears. It is the noise parameter that is one of the most appreciated and consequently influences the quality and competitiveness of the entire unit.
The potential source of noise is not only the gearbox but above all its integration into the overall plant. We recommend additionally minimizing potential sources of vibration by using experience from real applications by following the above procedures:
- By integrating a flexible coupling between the gearbox and the servomotor, the preload on the bearings that would result from misalignment of the reducer and coupling shafts is eliminated.
- If compactness is required, it is possible to manufacture the gearbox and the connecting parts as a compact unit. The precision of SPINEA® manufacturing technology allows us to minimize coaxiality.
- When connecting the reducer to the belt, it is important to make sure that the belt tension is correct.
- The non-aqueous adjustment of the control system constants generates vibrations during coasting and start-up. To reduce the vibration, it is necessary to implement gradual smooth start-ups and catch-ups.
- The servomotor should be oversized in proportion to the external load and the load on the gearbox. If the servomotor is undersized, it generates vibration at maximum torques.
- Any influence of axial force on the input shaft of the gearbox is inadmissible for standard reducer bearings. If an input gear is implemented that generates this axial force, it must be captured by a separate thrust bearing.
- The temperature is also an indicator of improper use of the reducer. As soon as the surface temperature is above the maximum permissible /65 °C/ it generates vibrations.
The solution is to introduce a cooling cycle into the surface of the reducer and thus remove the increased heat. It is also possible to reduce the load cycles and adjust them to the maximum temperature, or to integrate oil lubrication that will also cool - eliminating heat from the reducer contacts. Also, reduce the external temperature, or create a fan airflow to remove heat from the reducer surface in critical conditions.
- Increased vibrations can also be noted in resonance - stacking possible sources of the same frequencies and increasing the amplitudes of oscillation of the whole system.
The solution is to change frequencies from different sources or to bridge the resonance frequency band in an accelerated mode.
All recommendations related to external loads, maximum forces and temperatures are listed in the SPINEA® product catalogue or can be consulted directly with the sales department.
One direction regarding vibration is the reduction of the energetic effects of vibration = noise reduction, typical for today. A second direction, intensive for the future, is increasing the informative use of vibration as an identifier of the state of products in machines.
Frequency, vibration and noise are of great use: fault prediction, maintenance activity and equipment tribology. Filtering and understanding individual vibration frequencies is and will be a permanent part of Smart technologies that analyse in detail product wear, maintenance time, overall lifetime in relation to specific physical parameters of the load.
Artificial intelligence, connected to the "Internet of Things" and sharing of state reducers will bring self-learning systems that will operate more and more autonomously. Learning about the environment and adapting to it independently will be part of future technologies. In this process, vibrations and their individual frequencies will be key to understanding what is actually happening to the device.